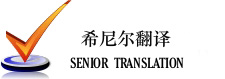
- 加入收藏
- 您可以撥打: +86 379 64122001
軸承中頻淬火工藝
后退中頻淬火工藝也叫感應(yīng)加熱工藝參數(shù)包括著熱處理參數(shù)和電參數(shù)。熱處理參數(shù)包括加熱溫度、加熱時(shí)間、加熱速度以及淬火層深度。電參數(shù)包括設(shè)備的頻率、零件單位面積功率等。
感應(yīng)加熱淬火工藝中幾個(gè)主要問題:
1、 確定零件的技術(shù)要求
表面淬火零件的技術(shù)要求包括:表面硬度、淬火層深度及淬硬區(qū)分布、淬火層組織等。
⑴. 表面硬度:感應(yīng)淬火后零件的表面硬度要求與材料的化學(xué)成分和使用的條件有關(guān)。
⑵. 淬火層深度:淬火層深度主要是根據(jù)零件的機(jī)械性能確定的。
⑶. 淬硬區(qū)分布:按零件的幾何形狀與工作條件的不同,各種表面淬火零件的硬化區(qū)部分和尺寸有不同的要求。
⑷. 金相組織:按零件的材料及工作條件,規(guī)定各格的等級(jí)范圍。按評(píng)級(jí)標(biāo)準(zhǔn)進(jìn)行金相評(píng)級(jí)。
2、 加熱溫度的選擇
感應(yīng)加熱速度快,與一般加熱相比,必須選用較高的加熱速度,適宜的加熱溫度是與鋼材的化學(xué)成分、原始組織狀態(tài)及加熱速度等因素有關(guān)。我車間由于設(shè)備的限制,只能采取目測(cè)加熱溫度的方法。
3、 設(shè)備頻率的選擇
頻率的選擇主要是根據(jù)淬火層深度和零件的尺寸大小來(lái)確定。當(dāng)設(shè)備給定或選定以后,設(shè)備的頻率就是一個(gè)不可調(diào)的參數(shù)。我車間的設(shè)備只有立式淬火機(jī)床一臺(tái),故工藝選擇中不再考慮設(shè)備頻率。
4、 感應(yīng)加熱方法及工藝操作
感應(yīng)加熱方法基本分為兩種:
⑴. 同時(shí)加熱法,這種加熱法是被加熱的表面同時(shí)共熱升溫,零件需要加熱的整個(gè)部分都被感應(yīng)器包圍著。在大批量生產(chǎn)時(shí),為充分發(fā)揮設(shè)備潛力,提高生產(chǎn)效率,只要設(shè)備輸出功率足夠的條件下,盡可能采用同時(shí)加熱。
⑵. 連續(xù)加熱法,零件表面的加熱和冷卻時(shí)連續(xù)不斷進(jìn)行的。連續(xù)加熱生產(chǎn)率較低,但加熱面積減小,設(shè)備的功率可以降低,因而擴(kuò)大了設(shè)備的應(yīng)用范圍。
5、 感應(yīng)加熱后的冷卻方式
冷卻方法有噴射冷卻、浸液冷卻、埋油淬火等。
⑴. 噴射冷卻,是常用的方法。我車間采用的是將冷卻液通過感應(yīng)器上的許多小孔,噴射到加熱面上,進(jìn)行冷卻。
⑵. 浸液冷卻,主要是用于同時(shí)加熱。零件表面同時(shí)加熱完畢后,立即將淬火部分浸入淬火槽中,進(jìn)行冷卻。如3B151-2-381錘頭,要求Φ60×110處表淬。加熱后直接進(jìn)入水中冷卻。
⑶. 埋油淬火,當(dāng)采用連續(xù)加熱法時(shí),為避免噴油時(shí)產(chǎn)生油煙,可將感應(yīng)器降至油面以下,進(jìn)行油面以下的連續(xù)加熱和冷卻。我車間就有我廠自行制造的埋油淬火機(jī)床。
6、 感應(yīng)淬火后的回火
感應(yīng)加熱淬火后,應(yīng)力分布不均,組織不穩(wěn)定。為了降低拉應(yīng)力,穩(wěn)定組織,達(dá)到所要求的機(jī)械性能,有必要進(jìn)行回火?;鼗鸱椒ㄓ校籂t內(nèi)回火,自回火和感應(yīng)加熱回火。
⑴. 爐內(nèi)回火:
在電爐內(nèi)回火,回火時(shí)間一般為1~2小時(shí),回火溫度按圖紙技術(shù)要求選擇。
⑵. 自回火
對(duì)于形狀簡(jiǎn)單,大量生產(chǎn)的零件可采用自回火。
⑶. 感應(yīng)加熱回火
感應(yīng)加熱回火時(shí),為了達(dá)到回火要求,回火時(shí)的加熱層深必須大于淬火層深,且必須采用相當(dāng)慢的加熱速度,故生產(chǎn)效率較低。如我車間承制的天車軌道,原來(lái)就采用感應(yīng)加熱回火,但效率太低,影響進(jìn)度,所以自行設(shè)計(jì)、制作了專用軌道回火爐,生產(chǎn)效率大大提高了。
感應(yīng)加熱淬火,加熱速度快,生產(chǎn)效率高,產(chǎn)品質(zhì)量好,但是技術(shù)含量也相對(duì)較高。所以只有將理論知識(shí)與生產(chǎn)實(shí)踐知識(shí)良好的結(jié)合起來(lái)才能夠很好的進(jìn)行以后的工作。
高頻淬火和中頻淬火的區(qū)別
1、高頻淬火淬硬層淺(1.5~2mm)、硬度高、工件不易氧化、變形小、淬火質(zhì)量好、生產(chǎn)效率高,適用于摩擦條件下工作的零件,如一般較小的齒輪、軸類(所用材料為45號(hào)鋼、40Cr);
2、中頻淬火淬硬層較深(3~5mm),適用于承受扭曲、壓力負(fù)荷的零件,如曲軸、大齒輪、磨床主軸等(所用材料為45號(hào)鋼、40Cr、9Mn2V和球墨鑄鐵)。
感應(yīng)加熱表面淬火,是利用電磁感應(yīng)、集膚效應(yīng)、渦流和電阻熱等電磁原理,使工件表層快速加熱,并快速冷卻的熱處理工藝
感應(yīng)加熱表面淬火時(shí),將工件放在銅管制成的感應(yīng)器內(nèi),當(dāng)一定頻率的交流電通過感應(yīng)器時(shí),處于交變磁場(chǎng)中的工件產(chǎn)生感應(yīng)電流,由于集膚效應(yīng)和渦流的作用,工件表層的高密度交流電產(chǎn)生的電阻熱,迅速加熱工件表層,很快達(dá)到淬火溫度,隨即噴水冷卻,工件表層被淬硬
表面淬火零件的中間熱處理是調(diào)質(zhì)
表面淬火 缺點(diǎn):處理復(fù)雜零件比滲碳困難
常用中碳鋼(0.4-0.5%C)和中碳合金結(jié)構(gòu)鋼,也可用高碳工具鋼和低合金結(jié)構(gòu)鋼,以及鑄鐵。
一般零件淬透層深度為半徑的1/10左右時(shí),可得到強(qiáng)度、耐疲勞性和韌性的最好配合。
對(duì)于小直徑10-20mm的零件,建議用較深的淬透層深度,即可達(dá)半徑的1/5;
對(duì)于截面較大的零件可取較淺的淬透層深度,即小于半徑1/10以下。
1,工作于摩擦條件下的零件,如一般小齒輪、軸
45、40Cr、42MnVB;高頻淬火,淬深1.5-2mm
2,承受扭曲、壓力負(fù)荷的零件,如曲軸、大齒輪、磨床主軸等
45、40Cr、65Mn、9Mn2V、球墨鑄鐵;中頻淬火,淬深3-5mm
3承受扭曲、壓力負(fù)荷的大型零件,如冷軋輥等
9Cr2Mo、9Cr2W;工頻淬火,淬深>=10-15mm
表面淬火、普通淬火后碳鋼的疲勞強(qiáng)度比較
含碳量% 熱處理方法 扭轉(zhuǎn)彎曲疲勞強(qiáng)度
0.33 高頻表面淬火 600
0.33 火焰表面淬火 350
0.33 電爐內(nèi)整體加熱淬火 90
0.41 高頻表面淬火 600
0.41 電爐內(nèi)整體加熱淬火 110
0.41 正火 130
0.63 高頻表面淬火 360
0.63 火焰表面淬火 390
0.63 電爐內(nèi)整體加熱淬火 15
- 聯(lián)系我們
銷售經(jīng)理:王經(jīng)理
移動(dòng)電話:18939000078銷售熱線
電 話:0379-64122001
0379-64122002技術(shù)中心
電 話:0379-64122008
電子郵箱:techsupport@sbi.com.cn
地 址:中國(guó)洛陽(yáng)市西工區(qū)河南洛陽(yáng)工業(yè)園區(qū)緯四路
傳 真:0379-64122006
電子郵箱:sbi@sbi.com.cn
-